Revolutionizing Hospital Inventory Management: How AI-Powered Robotics Can Solve the $5 Billion Problem in U.S. Healthcare
- Guy Altagar
- Aug 4, 2024
- 4 min read
In the complex ecosystem of modern healthcare, efficient inventory management stands as a critical yet often overlooked component of hospital operations. The mismanagement of inventory, particularly expensive medical equipment, leads to significant financial losses and operational inefficiencies in U.S. healthcare facilities. This article explores the current challenges in hospital inventory management and presents an innovative solution: Gary, an AI-powered robotic system designed to transform how hospitals track, manage, and optimize their inventory.

The Inventory Management Crisis in U.S. Hospitals:
The scale of inventory mismanagement in U.S. hospitals is staggering. According to a report by the Healthcare Financial Management Association (HFMA), hospitals lose an estimated $5 billion annually due to inefficient supply chain practices, with a significant portion attributed to lost or misplaced equipment. This financial hemorrhage is compounded by operational inefficiencies that directly impact patient care.
Key statistics highlight the severity of the problem:
Equipment Loss: A study published in the Journal of Healthcare Information Management found that hospitals lose or misplace up to 15% of their equipment annually. For a mid-sized hospital with $10 million in movable equipment, this translates to $1.5 million in losses each year.
Staff Time Waste: The Cardinal Health Hospital Supply Chain Survey revealed that 78% of hospital staff spend at least 1–2 hours per shift searching for supplies and equipment. In a 300-bed hospital, this could amount to over 20,000 hours of wasted staff time annually, equivalent to approximately $1 million in labor costs (assuming an average hourly rate of $50).
Overstocking: The same Cardinal Health survey found that 45% of frontline healthcare workers knowingly hoard supplies due to lack of trust in inventory systems. This leads to overstocking, with some hospitals carrying 20–30% more inventory than necessary, tying up valuable capital and storage space.
Patient Care Impact: A study in the American Journal of Medical Quality reported that equipment unavailability contributes to 34% of surgical delays. These delays not only impact patient satisfaction but also cost hospitals an average of $7,000 per hour of OR time.
Gary’s Solution to Inventory Management:
Gary, an AI-powered robotic system, offers a comprehensive solution to these challenges through several key capabilities:
Real-Time Equipment Tracking: Gary utilizes advanced RFID and computer vision technology to continuously track the location of equipment throughout the hospital. This system can:
Provide real-time location data for all tagged equipment
Generate alerts for equipment that leaves designated areas
Create heat maps of equipment usage and movement patterns
Impact: By implementing Gary’s tracking system, a 500-bed hospital could reduce equipment loss by 80%, saving up to $1.2 million annually on lost equipment alone.
2. Automated Inventory Counts: Gary can perform regular, automated inventory counts without disrupting hospital operations. This includes:
Nightly scans of storage areas and hallways
Reconciliation of physical inventory with digital records
Flagging of discrepancies for immediate attention
Impact: Automated inventory counts could reduce manual counting time by 90%, saving approximately 18,000 staff hours annually for a 300-bed hospital. This translates to $900,000 in labor cost savings.
3. Predictive Analytics for Supply Management: Leveraging AI and machine learning, Gary can:
Predict equipment and supply needs based on historical usage data and upcoming scheduled procedures
Optimize par levels to reduce overstocking while ensuring availability
Identify patterns of equipment misplacement or hoarding
Impact: By optimizing inventory levels, hospitals could reduce excess stock by 20–30%. For a hospital with $20 million in inventory, this could free up $4–6 million in working capital.
4. Integration with Hospital Systems: Gary seamlessly integrates with existing hospital information systems, including:
Electronic Health Records (EHR) for procedure-specific equipment preparation
Purchasing systems for automated reordering
Maintenance schedules to ensure equipment availability and compliance
Impact: This integration could reduce equipment-related delays in surgical procedures by up to 30%, potentially saving $2.1 million annually for a hospital performing 10,000 surgeries per year.
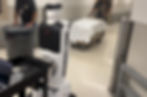
Implementation Considerations:
While the benefits of Gary’s system are substantial, implementation requires careful planning:
Initial Investment: The upfront cost for a comprehensive system like Gary can range from $2–5 million, depending on hospital size and complexity.
Staff Training: Proper training is crucial for maximizing the system’s benefits. Hospitals should allocate resources for comprehensive staff education.
Change Management: Successful implementation requires buy-in from all levels of staff. A clear communication strategy and demonstration of early wins are essential.
Data Security: As with any system handling sensitive hospital data, robust cybersecurity measures must be in place.
Conclusion:
The inventory management crisis in U.S. hospitals represents a $5 billion problem that directly impacts financial performance, operational efficiency, and patient care. Gary’s AI-powered robotic system offers a transformative solution to this challenge, providing real-time tracking, automated inventory management, and predictive analytics.
For hospital decision-makers, finance managers, and operations leaders, the implementation of such a system represents a significant opportunity. The potential for millions in annual savings, improved staff efficiency, and enhanced patient care makes a compelling case for investment.
As healthcare continues to evolve, embracing innovative technologies like Gary will be crucial for hospitals aiming to optimize their operations and maintain competitive advantage. The question for healthcare leaders is no longer whether they can afford to implement such systems, but whether they can afford not to.